Instrument Rebuild
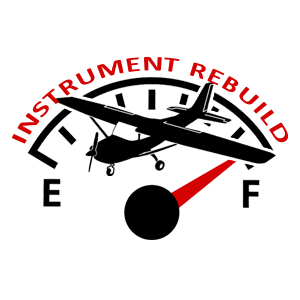
About Instrument Rebuild
HOW IT ALL STARTED
Many times the events of our youth, effect our whole future. This was true with Instrument Rebuild's, Paul Malkasian. It all started when Paul was 12 years old, his father was a poor immigrant. His father had a car that had a clock, of rare design, which was attached to the rear vision mirror. It was wound by pulling on a string, Paul pulled too hard one day and the string broke taking the main spring with it as well as the string for the recoil spring.
His father said, "Fix it yavrum (dear one). " ( His father always referred to his only son as dear one.) It seemed impossible, but his dad said. "Fix It." So he set out to fix it. He found another main spring in a (then) dollar pocket watch. and attempted to fix it. Paul struggled for days, and finally went to the adjoining town, Port Angeles (Washington), to a lady watchmaker. He was amazed when she showed him how to rewind the spring into the winding barrel.
His father had escaped from the horrors of the Turkish massacre of the Armenians. He was a cement finisher ( in those early days a lot was done on his knees) and a farmer. His life was hard. But he was free. He always referred to America as "God's Country." He would say, "This is God's Country." Paul had broken something he was proud of. He told him to fix it.
From that day on, clocks and watches became his hobby. He was fascinated with them. He fixed them for friends and acquaintances. Upon graduating from high school, and after much pleading with his mother, he journeyed to California, where he attended and graduated from the South Gate College of Watchmaking. Fortunately he had a sister who lived near the the school. His only expense was the school.
Now I'm sure you understand that I am talking about WATCH MAKING, not watch fixing. He learned to make the watch parts. he learned to examine and trouble shoot and most of all he learned to be observant and analyze.
The next step in his life was with Sperry Gyroscope Company, which later became Sperry Rand Corporation, and finally Sperry Flight Systems, where he learned to repair aircraft instruments, which he excelled in with his background of watchmaking. The secret was the detail he had been trained to notice. There were other secrets he had learned which I will not mention here. He eventually became North West Region Supervisor with 28 technicians.
After leaving Sperry, he established his own business. This was going nicely with all the previous contacts he had made, when he received a call from the Boeing Company. They needed someone to set up an instrument shop for a country to which they had sold airplanes. Being familiar with his expertise as he had worked closely on the delivery of new instruments they had purchased from Sperry. They knew his reputation as an instrument man. They needed an instrument shop set up so they called him. He found the prospect of traveling to Europe, and especially close to the country his parents came from, intriguing. He accepted.
After this assignment was completed, He stayed with the Boeing, for 14 years, trouble shooting for various contractors who were having difficulty with the production of acceptable product. One of those contractors was located in Phoenix, another was in Iowa, as well as others. Eventually he became a Quality Analyst.
His many experiences included going to Montreal Canada for a final inspection of the instrumentation of the U S Presidents new plane. His position had become Equipment Quality Analyst for the Boeing Company.
After Boeing, he started full time in his own business (repairing instruments for smaller planes rather then the large aircraft he had previously worked on), Instrument Rebuild. His expertise was widely known at this time with many flying clubs, including the Boeing Flying Cub as well as several Navy Flying clubs.
Instrument Rebuild was Incorporated -- as Malkasian Corporation, dba Instrument Rebuild and quickly became an FAA certified shop due to his education and years of experience. We like Hallmark's "When you care enough to send the very best." Call us when you "Care enough to want the very best." Ask us and we'll tell you why.
One of the more notable and challenging experiences he faced was testing 67,000 miniature light bulbs for the armed forces 1st response.
He called the Secretary of the Navy, a hard speaking individual to get instructions and to inquire as to the percentage rate allowed for failure.
There was silence on the line and Paul asked, "1% ?
There was silence on the line, then he was told, " You don't seem to understand, we want zero percent.
As any failure we have to abort the mission and come back to port.
Testing revealed that 200 of the lamps failed.
This process was accomplished by 3 of us, (including family) on a kitchen table. The testing process was developed by a dear friend who is no longer with us.
We'd probably still be testing if it hadn't been for the simplified system he developed for us. (No robots or automation.)